MAE: 494
GROUP 11

The prototype being built consist of two sections, the watering section and the central diverter. The components of the watering section consists of PVC pipe systems. The PVC was chosen because it is easy to work with and can withstand moisture without being weathered critically. The main use of PVC is for plumbing systems which led the group to unanimously choose this material for the water carrying pipes. The second part is the central diverter. This part was originally going to be cylindrical with a gear train, but we decided to go with simpler geometry and make it a box. The box will have solenoid valves to divert water from a bottom section instead and have a top section to house electrical system that will control this. The material poly carbonate clear plastic was chose for its strength and also for display capabilities, but any strong plastic can be used.
The prototype of the closed loop irrigation system will be used to test and validate each design requirement.
​
The system will be required to water an envelope land size of 2m x 2m. The prototype will be able to test this as the size of one quadrant will be 1m x 1m. If the system works correctly it will be able to water a 2m by 2m size when the last three quadrants are implemented.
​
To operate correctly the system must withstand 40psi, for this all that will be needed in to subject it to the 40 psi a garden hose can produce. Furthermore the system must water evenly and have a retention of 6.67 gallons. This can easily be observed with a grid of water catching devices to measure the dispersion.
​
The systems program should be able to run continuously without further input after starting, also it must be able to with stand outdoor conditions. Getting to a point where the program will be able to run automatically will just be trial and error. To test the resistibility of the system the prototype can be subjected to conditions that match different climates.
The system must be able to ping the sensors in a timed fashion while also running continuously. To accomplish this we can run the program for an extended amount of time to see if there are any faults in run time or ping timing.
​
The system as a whole must only use a set amount of power as to stay as efficient as possible. We can run the system for and elongated amount of time with a power source that has a known amount of power in it, then see if the power consumption matches up to the calculations.
​
The central diverter when not doing anything must have a water tight seal as to not waste water. This is simply tested by checking for leaks and correcting the problem. However, more importantly the diverter must be able to respond to a command to distribute water to a specific section within a given amount of time. Again easily tested by timing its response to a given command.
Prototype and Validation
PROTOTYPE UPDATE
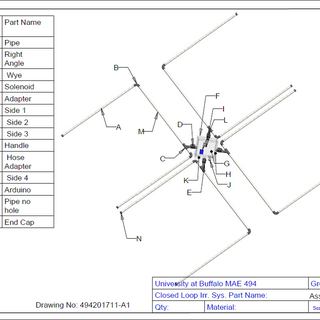
Prototype Progress
The prototype manufacturing has been moving along smoothly. The central diverter parts are all cut out and have the necessary holes drilled in. The PVC piping has been cut to length and has had the water dispersion holes drilled. For both sections all that needs to be done is the final assembly and gluing. Here are some photos of the parts and some machines we used to complete this.
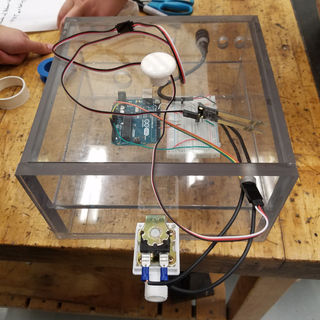
Video of Prototype
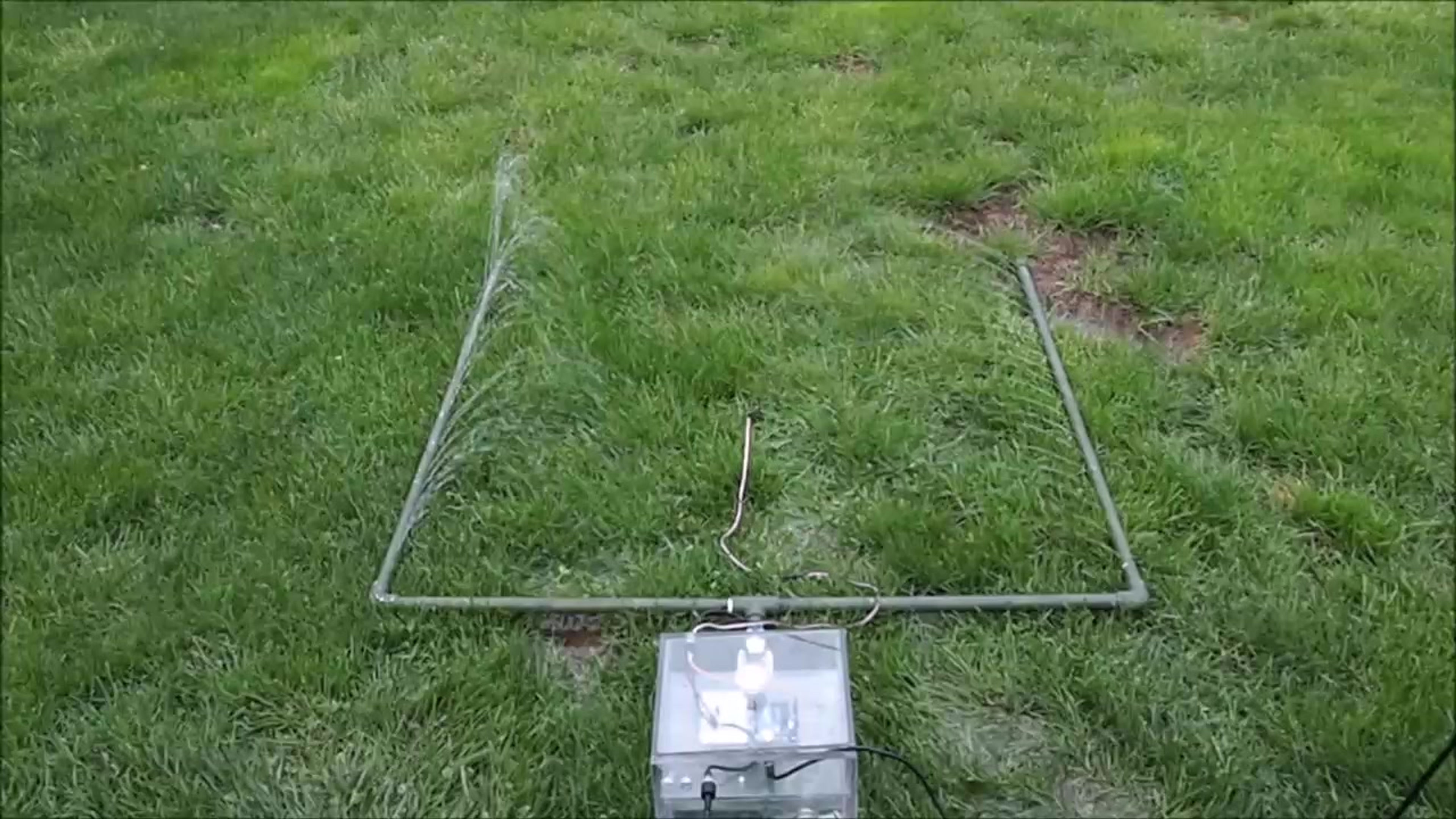