MAE: 494
GROUP 11

There must be an adequate amount of pressure in the hose to deliver a steady and strong stream of water to one zone at a time. A patent authored by W. Stark had a similar setup to ours, reporting that an adequate hose pressure was between 40 and 60 psi. If our water source has too much or little pressure, it can be adjusted with a valve between the water source and the central diverter.
Analysis of System
Water and piping
Electrical
The components that require electric power are the moisture sensors, the display screen, the Arduino, and the indexing motor. Everything should connect through the Arduino, and the Arduino to a computer via a USB cable. The computer should be able to provide all the power required for all the electronics. An additional power source can be added if the motor requires a larger power input than the Arduino can provide.
Thermal
The operating temperature of the central diverter is critical to the functionality of the system. Because these components will be subjected to many types of outdoor conditions, the electronic equipment (motor and sensors) should not overheat. The group will disregard freezing temperatures, because if the ground is below freezing, the user would most likely not be using the system anyway (it will be the user's responsibility to store/secure the electronics during the wintertime). To prevent this from happening, an alert should be sent to the user when the temperature of the system in within a dangerous range. While we could add a temperature sensor to the central diverter, the “danger zone” can be just as easily calculated using the thermal shock equation. So long as the relative robustness of the material is not reached, the system is “safe”.
Environmental
The prototype being built is a closed loop irrigation system. This system prototype requires piping and a water distribution box, also electrical components along with valves are required. Most of the prototype is made of different types of plastics mainly PVC and Polycarbonate. Sensors that are used are pre made a shipped along with the solenoid valves and electrical components. The system consists of around half custom components and half premade components. The polycarbonate, sensors, solenoid valves, and electrical components have a shipping distance of about four-hundred miles this sounds like a lot but is relatively small. All of the shipping transportation can be done easily by truck due to the relatively close proximity. As far as manufacturing goes only a few cuts need to be made in raw materials to get components of the right size. Assuming that on average a machine takes 1100 W/hr to run then if to make all cuts only takes 10 minutes the power consumption would only be around 185 watts. The rest of the manufacturing will be manual labor of gluing and fitting parts together. Also while cuts are made on the polycarbonate and PVC are made there will be excess material. However, both of these materials are recyclable and they should be properly separated to have this done. This prototype is very well designed in all aspects including environmental ideals. All materials will be used or recycled, on top of that shipping distance is small and will have a small impact on the environment. Not many tradeoffs can be made with the current materials as they are all needed and most can be recycled. Environmentally this prototype is in a good state.
Thermal Shock Equation

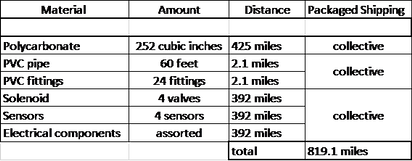
Environmental Impact Data
Economic
The economic analysis component examines the engineering development and manufacturing costs of our product. Material and labor costs are important in any design. In this age of manufacturing, it’s expected that labor costs and production time are kept to a minimum. Since our irrigation system will not be manufactured in a high volume production setting, the analysis will give a rough estimate on the product’s economic impact, as well as areas where the design can be improved upon within an economic scope, i.e. what changes could be made in future prototypes to decrease cost, increase profit etc. Overhead and design engineering cost will also be taken into consideration. A total cost summary will give the price of the product based on the cost analysis and the estimated life of the product. The group will only be manufacturing one zone of the system, but the economic analysis will be for the full, four-zoned product. Since the majority of our materials are plastics and electronics, the labor costs are divided between these two categories. Average U.S. wages in the plastics and rubber production industry is $21.39/hour. Wages in the computer and electronic production industry average $35.70/hour. Here, we will assume that assembly costs per hour are the same. We will estimate that the plastic parts would take 1 hour to manufacture and the electronic components 2 hours to manufacture (under skilled and professional production). Assembly time might be 1 hour for the plastic components (including glue drying time) and the electric components a half hour (soldering and integration into the diverter). Total labor costs could be estimated to be about $132.03. The majority of our machining will be done on a milling machine, drill press, and table saw. Since machine shops prices can have a very wide range, $60/hour seems like a reasonable estimate for the scope of our design and the types of cuts we are making. Since the PVC components can be done at the same time as the polycarbonate sheet, we can estimate the total active time of using the equipment to be 1.5 hours (manufacturing and assembly). Given the machining price of $90.00. Overhead and general and administrative are costs not related directly to manufacturing. Overhead covers expenses such as electricity, plant clean up, computer/software use, and support labor. In general, overhead costs can be estimated to be between 150-250% of the cost of a labor hour. Using the plastic manufacturing labor costs and an average percent of the overhead costs we have estimated overhead to be $42.78. Design engineering can also have a wide cost range with many variables affecting the price per hour. Contracting a junior engineer can cost upwards of $90/hour depending on their skill level, expertise, and experience. This final price for the design cost is hard to estimate. With a group of five students working on this design for almost two semesters, if we were actually paid for our time spent on the project, the cost would be very high. A professional team of engineers working solely on this project, full time, might take anywhere from a few days to months to get a working prototype.

